Refrigeration Breakdown Horror Stories: Why Regular Inspections Matter
- Key Deer Mechanical
- Feb 4
- 3 min read
Updated: Feb 17
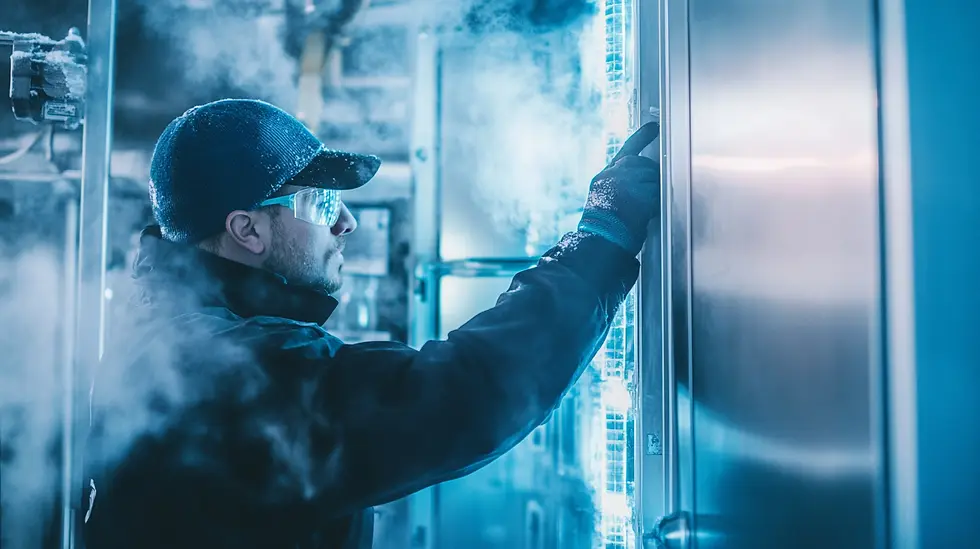
When it comes to refrigeration systems, most property managers and trucking companies adopt the classic "if it ain't broke, don't fix it" mentality. But here's the thing—by the time it is broken, you're likely knee-deep in melted ice cream, spoiled seafood, or worse, a lawsuit. Refrigeration breakdowns aren't just an inconvenience; they're a nightmare waiting to happen. Let us walk you through some real-life horror stories to prove why regular inspections aren’t optional—they’re essential.
The $50,000 Sushi Disaster
A high-end Florida restaurant boasting a premium sushi menu thought skipping regular maintenance on their walk-in freezer was a "cost-saving" strategy. Spoiler alert: it wasn’t. One sweltering summer night, their refrigeration system decided to call it quits, and by morning, thousands of dollars’ worth of tuna, salmon, and uni were ruined. Not only did they lose inventory, but their kitchen had to shut down for days to repair the damage and restock—resulting in an estimated $50,000 in losses.
But wait, it gets worse. A health inspector showed up unannounced the same week and found improperly stored food due to temporary cooling solutions. Result? A public health violation and a one-star Yelp review that went viral. All of this could have been avoided with regular preventative maintenance.
Frozen Cargo Goes Up in Smoke
Let’s talk about the trucking industry, where refrigeration units are the lifeline for reefer trucks. One unlucky driver transporting frozen goods across Florida’s alligator-infested highways ignored the warning signs of a failing reefer unit. Halfway through the trip, the unit broke down in the middle of July. By the time they got to the destination, the entire shipment of frozen goods had thawed and spoiled. The client refused the delivery, and the trucking company was left eating a $75,000 loss.
What’s maddening? A quick inspection could have identified the failing compressor before it turned into a catastrophic failure. But hey, why spend $200 on a maintenance check when you can lose a six-figure sum instead?
The Great Refrigerant Leak Cover-Up
Here’s where things get controversial. Many properties and businesses operate with outdated refrigeration systems that still use R-22, a refrigerant that’s been phased out due to its devastating environmental impact. Ignoring a refrigerant leak isn’t just bad for the planet; it’s bad for your business.
Case in point: A boutique hotel in Miami Beach ignored minor refrigerant leaks in their cooling systems for months. Eventually, the leaks escalated, leading to skyrocketing energy bills and an HVAC system operating at half its efficiency. By the time they called for emergency repairs, the refrigerant levels were dangerously low, and the system required a complete overhaul. Cost? Over $100,000. Oh, and let’s not forget the EPA fines for failing to address refrigerant leaks in a timely manner.
Why Regular Inspections Are Non-Negotiable
Still think skipping inspections is worth the risk? Here are some cold (pun intended) hard facts:
90% of refrigeration breakdowns are preventable with regular maintenance, according to industry studies.
Refrigeration systems that receive regular inspections operate at 20-30% higher efficiency, saving thousands in energy costs annually.
Ignoring minor refrigerant leaks can lead to fines of up to $37,500 per day for non-compliance with EPA regulations.
But Let’s Be Honest: Why Do People Skip Maintenance?
Here’s the uncomfortable truth: many businesses skip maintenance because they think they’re saving money. The reality? They’re gambling with their bottom line. It’s the ultimate case of penny-wise, pound-foolish.
Some argue that maintenance contracts are a scam, claiming, "Why pay for something that might break when it hasn’t yet?" This mindset is precisely why businesses find themselves scrambling during emergencies, paying double or triple for last-minute repairs or replacement systems.
How Key Deer Mechanical Can Save the Day
At Key Deer Mechanical, we’re in the business of preventing these horror stories from becoming your reality. Our preventative maintenance programs are designed to catch small issues before they snowball into catastrophic failures. Here’s what we offer:
Comprehensive inspections for HVAC and refrigeration systems to identify potential problems early.
Regular maintenance schedules tailored to your specific needs, whether you manage a hotel, restaurant, or trucking fleet.
Expert technicians who ensure your systems are compliant with EPA regulations, avoiding costly fines.
Cost-effective solutions that save you money in the long run.
Don’t Be the Next Horror Story
The moral of the story? Refrigeration maintenance isn’t a luxury; it’s a necessity. Ignoring it can cost you far more than a simple inspection ever would. So, do you want to be the sushi restaurant out $50,000, or the trucking company stuck with spoiled goods? Or do you want to be the smart business owner who plans ahead, saves money, and keeps things running smoothly?
The choice is yours. But if you want to sleep at night without worrying about your refrigeration system giving up on you, give Key Deer Mechanical a call. We’ll make sure your story is one of success—not disaster.
Comments